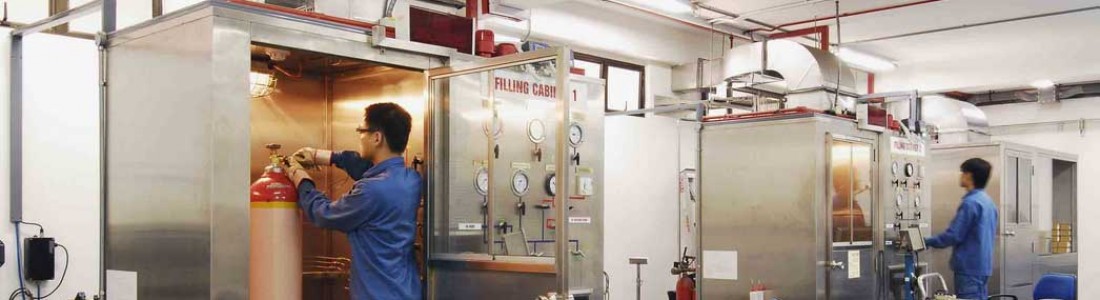
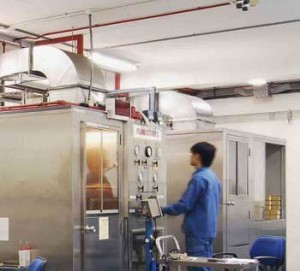
Accuracy = k[(std. error)^2 + (precision)^2 + (cal. curve)^2]^1/2
Here is an example of this calculation using a coverage factor of k = 2 and a 95% confidence level:
At 1RSD:
Standard error = 0.5%
Precision = 0.5%
Calibration curve error = 0.5%
The result of the calculation is 1.7%. Commonly a supplier will round that value to a +/- 2% accuracy value.
In the specialty gas industry, accuracy calculations are not the only methods used. Some suppliers may use other formulas and methods for calculating accuracy such as gravimetric additions. When ordering calibration gas standards, you must consider the measurement accuracy needed for each application. Using process control charts, it is possible to determine the impact of accuracy deviations. For example, a +/- 2% accuracy value for an individual certified standard could produce a range of cylinder values anywhere from -2% to 2% and for repeat orders 4%. In some cases, the required accuracy and the correct procedure for certifications will be determined by environmental regulations. An example of this would be EPA Protocol gases that are used for environmental instrumentation calibrations. It is imperative that the propagation of error calculation is accurate when working with processes or mixtures that utilize software to perform dewpoint calculations. This is because calculations done manually are not able to take into consideration molecular interactions that can reduce the allowable cylinder fill pressures. It is also important to consider mixture storage in relation to the mixture stability or shelf life. For gas standards that must comply with environmental regulations and for ISO 9000 compliance, the certificate of analysis must also report the shelf life. EPA Protocol mixture shelf lives are specified by the U.S. EPA. In the case of other gas mixtures, the study of the mixtures and reporting must be performed by individual suppliers. Some stability of mixtures can vary dramatically between suppliers depending on the technology they are using, for example, when measuring stability of reactive gases at concentrations below 1000ppm.
When ordering calibration gas standards, you must consider the measurement accuracy needed for each application.
Accuracy refers to the degree of closeness between a predicted value and the actual measured value. Accuracy may also be referred to as certification accuracy, analytical accuracy, or analytical uncertainty. All standard gases used for calibration provide certified values for the concentration of components in the gas, along with a description of the accuracy of the certified values. When calculating accuracy, the formulas that are generally accepted are found in the ISO (International Standard Organization) and also in institute papers in the U.S. In addition, accuracy calculations must also take in to account the propagation of uncertainty or the propagation of error. Propagation of uncertainty is the effect of the uncertainty of variables on a calculation, for example, instrumentation precision. Typically, this is calculated using the square root of the total of the squares of the values of the common errors. When measuring for the certification of calibration gas standards, the common errors taken into account are the calibration curve error, reference standard error, imprecision of measurements, and instability of the gas mixture. For certifying a gas mixture against a reference standard, this is the equation used and it assumes that there is no instability over time.
Accuracy = k[(std. error)^2 + (precision)^2 + (cal. curve)^2]^1/2
Here is an example of this calculation using a coverage factor of k = 2 and a 95% confidence level:
At 1RSD:
Standard error = 0.5%
Precision = 0.5%
Calibration curve error = 0.5%
The result of the calculation is 1.7%. Commonly a supplier will round that value to a +/- 2% accuracy value.
In the specialty gas industry, accuracy calculations are not the only methods used. Some suppliers may use other formulas and methods for calculating accuracy such as gravimetric additions. When ordering calibration gas standards, you must consider the measurement accuracy needed for each application. Using process control charts, it is possible to determine the impact of accuracy deviations. For example, a +/- 2% accuracy value for an individual certified standard could produce a range of cylinder values anywhere from -2% to 2% and for repeat orders 4%. In some cases, the required accuracy and the correct procedure for certifications will be determined by environmental regulations. An example of this would be EPA Protocol gases that are used for environmental instrumentation calibrations. It is imperative that the propagation of error calculation is accurate when working with processes or mixtures that utilize software to perform dewpoint calculations. This is because calculations done manually are not able to take into consideration molecular interactions that can reduce the allowable cylinder fill pressures. It is also important to consider mixture storage in relation to the mixture stability or shelf life. For gas standards that must comply with environmental regulations and for ISO 9000 compliance, the certificate of analysis must also report the shelf life. EPA Protocol mixture shelf lives are specified by the U.S. EPA. In the case of other gas mixtures, the study of the mixtures and reporting must be performed by individual suppliers. Some stability of mixtures can vary dramatically between suppliers depending on the technology they are using, for example, when measuring stability of reactive gases at concentrations below 1000ppm.